The correct installation of the control valve is as important as the correct selection. The quality of the installation relates to the operating performance of the control system, control of quality, safety and cost, and so should be taken seriously. Control valve installed at the scene, the fire, explosion-proof, anti-leakage and put forward higher requirements, control valve noise pollution is also increasingly subject to the relevant departments. First, the control valve installation and construction requirements: Installation and construction of the general provisions: 1, control valve installation should be in accordance with the provisions of the design drawings and design documents. 2, the installation of control valves should comply with the relevant national standards, for example, construction and installation quality inspection and evaluation standards, industrial automation instrumentation and acceptance of construction specifications, installation of electrical equipment construction and acceptance of norms. 3, the installation of control valves required equipment, auxiliary equipment and main materials should be consistent with existing national or ministerial standards of the relevant provisions. Second, the installation and construction precautions: Control valve installation precautions should be easy to operate, safety and standardization considerations. The details are as follows. (A) Control valve installation location and orientation: 1, in accordance with the provisions of the design drawings and design documents, the installation location should have sufficient space for installation, operation and maintenance; its location should be avoided in a vibration, humidity, It is susceptible to mechanical damage, strong electromagnetic interference, high temperature, severe temperature changes and corrosive gas. The installation should be firm and smooth. The installation position should be such that the control valve actuator is above the adjustment mechanism. Figure 6-8 shows the straight Travel control valve of the various installation orientation. Among them, the location is the preferred location, second choice location. 2, the control valve fluid flow control valve fluid flow direction should be consistent with the arrow marked on the valve body. Under special circumstances may not be subject to the provisions of the restrictions. 3, the control valve connected to the control valve threaded connection, flange connection and welding connections. Threaded connections for small-diameter control valves, installation of threaded control valve, you must also install a removable removable connector. Flanged flange connection and clamping connections are two kinds, connecting the nominal diameter of the flange should be consistent with the control valve take over diameter. Flanges also have different pressure levels, flange pressure level should be consistent with the control valve pressure level. The inner diameter of the flange should be equal to the inner diameter of the pipe. Flange and pipe axis perpendicularity allowable deviation of l °. Flange sealing surface should be flush. Flange and pipe coaxial tolerance t should meet: t ≤ 0.015D (1 / β) (6-27) Where, D is the pipe diameter; Xi is working conditions under the throttle diameter and the pipe diameter ratio . Flange connection should be force appropriate, to avoid excessive local pressure. Try to avoid the use of welded connections, welding connections must be installed at the same time removable removable connectors. When connecting the control valve, the inside of the connecting pipe should not be caused to have new bulges. For example, gaskets, weld seams, etc. should not protrude in the pipe. 4, the control valve and the upstream and downstream shut-off valve, bypass valve connection control valve, the downstream shut-off valve and bypass valve should be installed with the control valve. The length of the pipe between the upper and lower shut-off valves and the control valve should take into account the resistance of the pipe and the effect on the fluid flow. Long straight pipe length is conducive to the stability of the fluid after the shut-off valve, the fluid flow can be smooth, reducing the impact of turbulence and reduce noise; straight pipe length is short, the fluid has not stabilized after the shut-off valve into the control valve, the noise enhancement , But the short pipe length helps to reduce the pipeline resistance and increase the pressure drop at both ends of the control valve so as to reduce the distortion of the flow characteristics and is in favor of the stable operation of the control system. Therefore, it should be weighed and considered. Normally, there should be 10D ~ 20D straight pipe on the upstream side and 3D ~ 7D straight pipe on the downstream side. D is the pipe nominal diameter, if necessary, should be set rectifier device. (B), the choice of connection options. 1, the control valve and the upstream and downstream shut-off valve connection in a variety of ways, several commonly used connection options. In the picture, scheme A has a compact structure, small footprint, easy maintenance and operation, and the system is easy to empty or drain. But often can not meet the enough length of straight pipe, resulting in increased noise. Program B structure covers a larger area, the control valve position can be installed in the lower or upper part, easy to adapt to operational requirements, but the length of straight pipe is not easy to guarantee. The structure of scheme C is suitable for the angle control valve, can reduce the number of elbows, covers a smaller area. On the bottom into the side of the flow, there may be a longer upstream straight pipe length. The structure of program D is similar to that of program B and covers a large area. The structure of the solution E is suitable for the angle valve. Compared with the solution C, the length of the straight pipe section on the upstream side is shortened, which is not conducive to the stability of the fluid. The structure of Scheme F is the most common connection structure. It covers a large area, the pipeline resistance is small, but the operation and maintenance space is small. 2. Discharge valve, vent valve, drain valve connection, in order to facilitate the removal of the control valve should be carried out before the demolition of the valve before and after the pressure relief valve, the relief valve should be installed in the control valve and the upstream and downstream shut-off valve between. 3, vent valve, drain valve for the discharge of fluid entrained non-condensable gas and condensate. Installation, the controlled fluid, gas or steam, in order to facilitate the condensate discharge, the sewage valve should be installed in the lowest control valve group. Controlled fluid is a liquid, in order to facilitate the non-condensable gas vent, vent valve should be installed in the highest point of the control valve group. 4, bypass valve. Control valve removal and maintenance, the bypass valve can be used to operate the production process. When charged with excessive traffic. With the control valve can not be properly adjusted, as a contingency measure, bypass valve can also be used as a control valve of the parallel connection program, the process control. To reduce costs, large-caliber control valve installed hand wheel actuator, can replace the bypass valve to operate. Bypass valve installation should be easy to operate, with the control valve, the downstream cut-off valve together to form a control valve group, therefore, should be installed with them, and at the same time to complete the construction and installation. The nominal diameter of the bypass valve is the same as the nominal diameter of the pipe, and the withstand voltage level is also consistent with the withstand voltage of the process. 5, the installation of the implementing agencies Usually, the implementing agencies and the control valve body directly connected, but the hydraulic actuator, long-stroke actuator and other implementing agencies and control valve body separately, the installation of implementing agencies should be noted that the implementing agencies with Rod and mechanical moving parts should be flexible, no loose or stuck and so on. Linkage length should be stable throughout the trip range, flexible and reliable. When connected to the control valve body with thermal displacement of the process piping, the relative position between the actuator and the valve body should be maintained. The handwheel actuator has side and top two, the installation should be left space for operation. Handwheel operation should be flexible, there is no stuck or reversed phenomenon. Should handwheel direction of rotation and valve opening relationship between the label. Limit devices should be adjusted to play a protective role. The hydraulic actuator should be lower than the controller installation, if it must be higher than the controller, the height difference should not exceed 1.0m, and should be installed in the pipeline gas exhaust valve, close to the controller installed check valve or Automatic shut-off valve. 6, the valve positioner installation Valve positioner valve position detection device and control valve stem or valve shaft directly connected, therefore, the installation should ensure that the feedback signal can be correct, timely reflect the valve position signal and changes. Normally, the valve positioner is supplied with the control valve, and both are connected by the manufacturer. When the production process control valve positioner needs to be added, it should ensure that the valve positioner valve position detection device action is correct, reliable and flexible. Feedback lever fulcrum mechanical gap should be as small as possible. Valve positioner signal lines should be properly connected, the gas source and output lines, input lines should be marked nameplate. Valve positioner valve position display signal should facilitate the operation and maintenance personnel to observe. 7, Other Accessories Installation Other accessories include valve position sensor, solenoid valve, limit switch, relay, electrical converter, the installation should comply with the relevant provisions of the product manual. Small flow control valve should be installed upstream filter. Serious turbulence, should be installed in the upstream rectifier device.
Forging Mold Development
Forging die is the basis for realizing forged products. Without good and superior molds, there is no way to produce qualified products. From mold design, to mold material selection, to mold manufacturing, every step is very critical. First of all, mold design should follow good performance, excellent processing performance and certain economic performance, and at the same time, molds with good formability, reasonable life, and easy installation, debugging and maintenance should be designed. For the selection of mold materials, reasonable and economical mold materials should also be selected according to product structure, batch requirements, etc. In the process of mold processing, the mold should be processed reasonably according to the precision requirements of the product, and the heat treatment and stress should be considered. Only by making adequate preparations can a reasonable and excellent mold be manufactured.
SCZY has its own internal mold manufacturing department, from mold design, material procurement, mold manufacturing are all handled internally by us. It can better and more effectively ensure the rationality of the mold and the performance of the mold. Can better communicate and coordinate with the production department to achieve the best results.
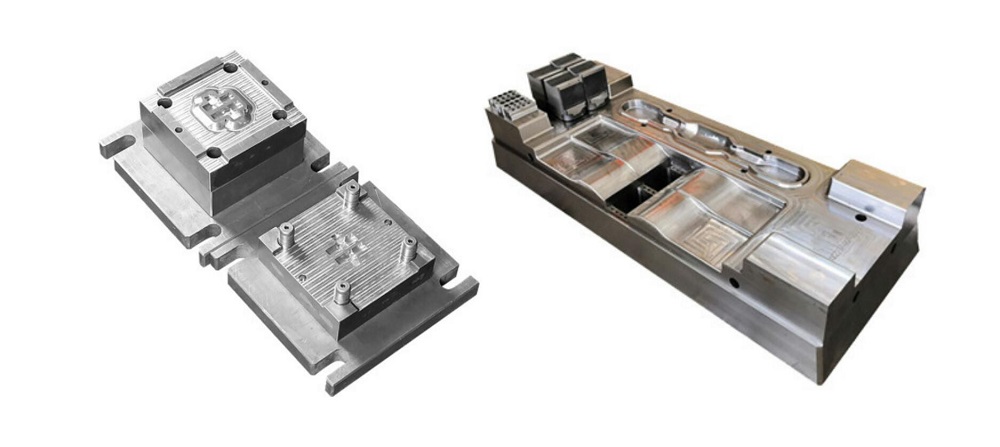
Forging Mold Development,Precision Forging Dies,Precision Forging Tools,Precision Forging Molds
Shenzhen SCZY Technology Co.,Ltd , https://www.szsccasting.com