Â
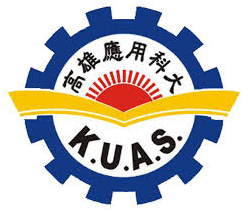
- Customer:Kaohsiung University of Applied Sciences
Plastics Precision Laboratory (PPL) - Industry:Research & Education
- Solution:Moldex3D eDesign / Injection Compression Molding (ICM) Module
- Region: Taiwan
- View PDF Version
Executive Summary
As the technology continues to evolve, using plastics to produce optical parts, such as a vehicle headlight lens(Fig. 1) has become a popular replacement for a complex and expensive glass manufacturing. However, due to the geometry and uneven thickness design of a headlight lens(Fig. 2), it is very likely to lead to undesirable product defect problems caused by uneven heat dissipation between the core and the surface layer of the part when using traditional plastic injection process to manufacture the part. Thus, apart from the traditional plastic injection molding, using Injection Compression Molding (ICM) might be a viable solution to better resolve product defect problems. In this case, PPL utilized Moldex3D’s Injection Compression Molding (ICM) simulation capability to study the possibility of adopting ICM to manufacture a vehicle headlight lens and further they were able to fine-tune the processing parameters for product optimization based on the simulation results. Moldex3D’s ICM simulation results enabled PPL to fully understand ICM process, and PPL was able to demonstrate the competitive advantages of using ICM in producing headlight lens. That is, with the help of Moldex3D simulation analyses, PPL was able to successfully prove Injection Compression Molding (ICM) a viable option for headlight lens manufacturing in their research.
       Â
      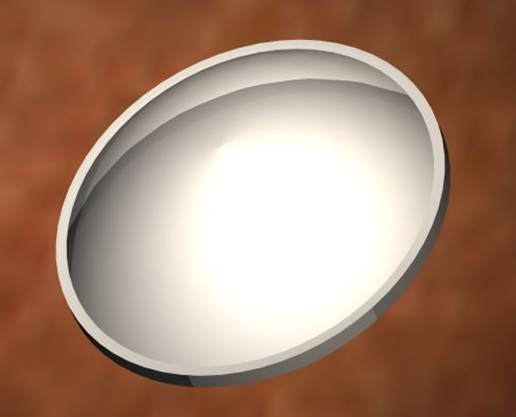
                        Fig. 1  A headlight Lens                                  Fig. 2  Part Design
Challenges
- Poor optical properties
- Warpage problem
- High product shrinkage (Fig. 3)
- High residual stress concentration in the gate region (Fig. 4)
Fig. 3 Â Moldex3D analysis indicates severe product shrinkage
in the core region due to uneven thickness design and heat dissipation.
        Â
Fig. 4 Â Moldex3D Optical Analysis indicates a high residual stress concentration in the gate region
Benefits
Through Moldex3D simulation analyses and the actual mold-trial results, PPL was able to successfully prove Injection Compression Molding (ICM) a viable solution to improve product quality.
- The product shrinkage was improved by 44%
- The warpage was improved by 29%
- The fringe pattern and the residual stress were more uniform. Thus, the overall optical properties of the part were greatly improved.
Case Study
Apart from using traditional injection molding process, PPL proposed to use Injection Compression Molding (ICM) to better address the product defect issues in order to improve the overall product quality.
There are several reasons why ICM is believed to be a better option for producing a headlight lens:
   1. Reducing injection tonnage
   2. Reducing residual stress
   3. Reducing molecular orientation
   4. Uniform packing pressure to reduce shrinkage
   5. Reducing sink marks and warpage
   6. Improving optical birefringence performance
   7. Easing specific volume variation
   8. Improving part dimensional precision
The objective of this case was to utilize Moldex3D Injection Compression Module to study the possibility of adopting ICM to manufacture a headlight lens. The case focused on 3 major influential factors: warpage, volumetric shrinkage, and optical properties and compared the differences between using traditional Injection Molding and Injection Compression Molding (ICM). The simulation results validated by the actual mold-trial results both confirmed the better competitive advantages of using ICM process and its significant improvements on product quality.
First of all, through Moldex3D warpage analyses, PPL was able to understand that due to the uneven part thickness design, using traditional plastic injection molding process may encounter product defects such as warpage and residual stress concentration induced by uneven heat dissipation between the core and the surface layer of the part. When applying ICM process, uniformly acting holding pressure was distributed throughout the whole cavity during the compression stage; thus, the required injection pressure could be reduced. This molding advantage could greatly reduce the warpage induced by uneven pressure distribution. Fig. 5 & Fig. 6 showed a conspicuous 29% improvement in the maximum warpage amount from 0.7mm to 0.5mm.
Fig. 5 Â Using Injection Molding process-The maximum warpage amount
was around 0.7mm (excluding gate and cold slug well).
Fig. 6 Â Using ICM process-The maximum warpage amount was around 0.5mm (excluding gate and cold slug well).
Next, according to Moldex3D simulation results, the heat was concentrated in the core region of the part, and the volumetric shrinkage was at a high level of 12%, indicating a severe shrinkage defect when using traditional injection molding (Fig. 7). On a contrast, a more uniform temperature distribution was observed in the core region when applying ICM process, showing a significant improvement in product shrinkage by 44% (Fig. 8).
            Â
          Â
Fig. 7 Â Using Injection Molding process-The shrinkage ratio in the core region was 12.1% (top).
The volumetric shrinkage of the actual product was -862.4µm (bottom).
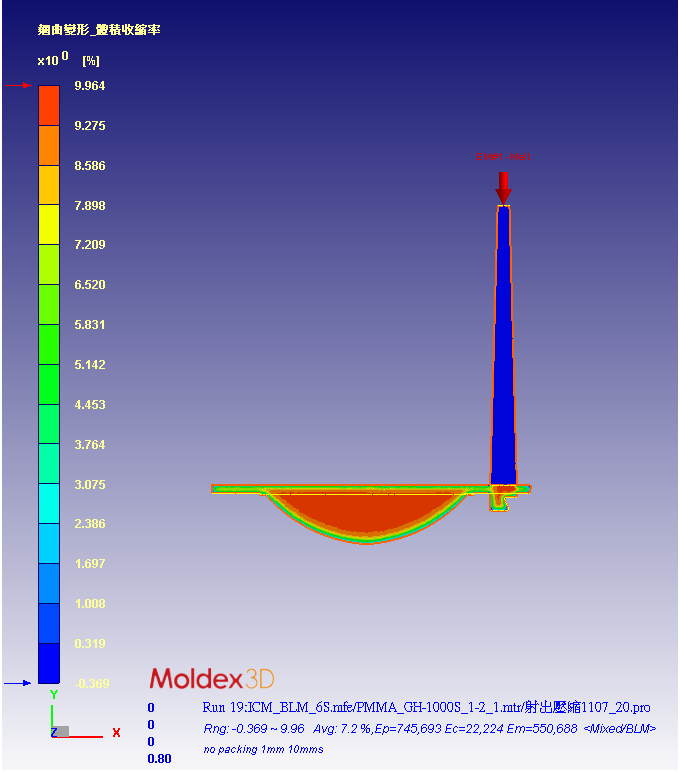
Fig. 8 Â Using ICM process-The maximum shrinkage ratio was 9.96% (top).
The volumetric shrinkage of the actual product was -490.5µm (bottom).
Comparing the fringe pattern analyses, the intense fringe patterns were observed in the gate region resulting in poor optical properties (Fig. 9). However, when applying ICM process, the optical properties were greatly improved. This was due to the fact that the in-mold compression can help lower the pressure, making the residual stress near the gate region more evenly distributed (Fig. 10).
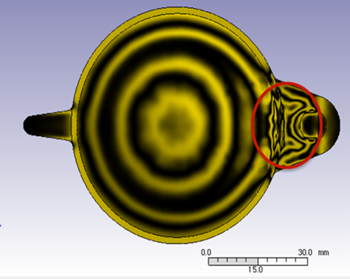
Fig. 9 Â Using Injection Molding process-The intense fringe patterns were observed in the gate region (top).
The photoelastic stress measurement showed a poor optical path length (bottom).
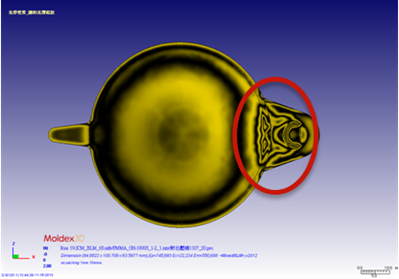
Fig. 10 Â Using ICM process-The fringe patterns observed were more evenly distributed (top).
The photoelastic stress measurement showed a significant improvement on optical properties (bottom).
Lastly, with the help of Moldex3D simulation analyses, PPL was able to get an in-depth look at the ICM process and evaluate the potential problematic areas. The important processing parameters for example, injection/compression switch point, compression force, compression speed, and stress distribution were carefully examined and optimized to achieve the best quality results.
Results
The Moldex3D simulation results assisted PPL to get a better understanding of the plastic flow behavior in the cavity when using both traditional injection molding and Injection Compression Molding (ICM). Its accurate prediction of ICM process not only proved it a viable solution for headlight lens manufacturing, but also enabled an effective optimization of the processing parameters that ultimately led to a significant improvement on the final product quality in order to meet the stringent product requirements.
high speed mixing granulator,wet material rotary granulator,screw extrude granulator
Jiang Yin Jun Lang Machinery Co.,Ltd , https://www.fluidbedgranulator.com