With the continuous development and advancement of mold industry technology, new materials and new processes are emerging. Selecting the right cutting fluid during mold processing is crucial to ensure product quality, increase processing efficiency, and reduce environmental pollution.
The most basic functions of metalworking fluids are lubrication, cooling, chip removal and protection. These four properties are not completely isolated. They have both a unified surface and an opposite surface. Such as cutting oil lubrication, anti-performance is good, but poor cooling, cleaning; aqueous solution, cooling, washing performance is good, but poor lubrication and anti-performance.
It is generally believed that in the low-speed heavy-load cutting machining (thread cutting, reaming, and tooth cutting), sufficient lubrication is required, and the extreme pressure cutting oil is usually selected. The main task of the cutting lubricant is to reduce the adhesion between the advancing surface and the chips. , as a boundary lubricant. In high-speed shallow cutting, cooling is the first choice. Water-based cutting fluid is generally used. Its main function is to reduce frictional heat and to remove heat. Those machining fluids that are difficult to reach the shear zone cause great difficulty in lubrication and cooling. Generally, suitable cutting fluids are carefully selected for reaming, gear cutting (especially hobbing), deep-hole drilling and boring, tapping (especially blind holes), deep-set holes, and threading.
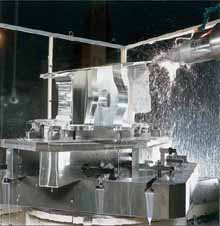
Fig. 1 The application of metalworking fluids in production shows that the use of suitable metalworking fluids can reduce the cutting temperature by 60~150°C, reduce the surface roughness by 1~2 grades, reduce the cutting resistance by 15~30%, and double the improvement. The service life of the cutters and grinding wheels, as well as the removal of iron chips and ash from the cutting area, increases the productivity and product quality.
In the mold processing process, the role of the tool is to cut off the processed material with a strong shear force in the main shear zone. Between the advancing surface of the tool and the exposed fresh metal surface, the thrust surface is subjected to high stress due to the strong adhesion. The cutting flaking due to cutting cuts through the tool advancing surface, creating a second shear zone - the shearing action of this area gives the tool maximum friction. At this time, the importance of lubrication and cooling is highlighted at the same time. It is worth noting that there are many types of metal removal machining, and each has its own unique working conditions.
The following will focus on the application of metalworking fluids in three specific processing methods, and combined with the user interview reports of Shell, De &22269, and OEL-HELD in this publication to illustrate the specifics of metalworking fluids. Application and performance requirements.
EDM
Shell's Wanan EDM110 and 130 are high-quality spark erosion machining oils (see Table 1, continued on the next page). They are made of paraffin-based base oils with high precision refining and very low aromatic content, good insulation properties, and product processing. High precision, long life, little skin irritation. Among them, the former has a medium viscosity and is suitable for spark erosion processing; the latter has a high viscosity and is suitable for high precision machining of spark erosion. Both of these products can also be used as tool grinding oils.
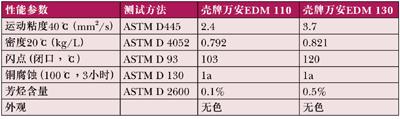
Table 1 Typical Value of Shell EDM 110/130 Spark Erosion Process Oil
Shell Wanan EDM110 and Shell Wanan EDM130 have some of the same features: low viscosity, excellent cleaning of workpieces and spark plugs; good chip resistance, extended electrode life; good insulation, high dielectric strength, surface finish High precision, processing surface roughness can be as low as 3 microns to lower; high flash point, can reduce the risk of fire in the machine; high boiling point, minimize volatilization losses, prevent oil viscosity due to volatile loss and processing accuracy Drop; good thermal stability and oxidation stability, long service life, not easy to oxidation and discoloration; colorless and odorless, help users to observe the process of spark plug processing; good filterability, rapid removal of fine processing Crumbs; aromatics content is extremely low, little effect on skin irritation, harmless to the human body.
User testimonials
Shell metal processing oil / liquid performance, product life cycle. In this regard, BYD Precision Manufacturing Co., Ltd. Equipment Department Zhang Qibo has a deep understanding.
According to Zhang Qibo, BYD precision manufacturing is one of the top three mold manufacturing bases in South China, and its equipment department has hundreds of well-known brand machine tools. The company's current use of Shell Spark Erosion Process Oil has been over three and a half years, and it has no discoloration or taste change. With such a long service life, BYD Company has not only reduced the procurement cost of oil products, but also effectively reduced equipment downtime due to oil changes, thus realizing improved production efficiency.
Not only that, the use of Shell spark erosion processing oil, also provides an effective guarantee for BYD's production safety. BYD's technicians had done such an experiment—the use of cloth strips to dip shell sparks to etch the oil, and then tried to light it, but after many tests, the strips could not be burned. It can be seen that compared with other kerosene spark erosion processing oils, Shell spark erosion machining oil has stable performance and is a reliable guarantee for safe production.
Grinding
The friction between the abrasive particles and the metal surface during the grinding process generates a lot of heat. When the heat is accumulated to a certain degree (the instantaneous temperature of the grinding point can reach 1500°C, and the average temperature of the grinding area of ​​the abrasive and the workpiece is between 500°C and 800°C), the surface of the workpiece will be burned or even deformed. The surface quality and accuracy will be affected. If the operating conditions of the grinding process are improved and the grinding oil is used for sufficient cooling and lubrication, half of the thermal energy in the process will be absorbed by the coolant, and the final heat input to the workpiece will only account for 15% of the heat energy generated during the entire process. . Therefore, the grinding oil effectively reduces the chance of the workpiece being burned.
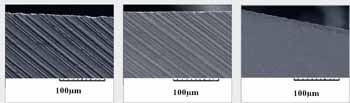
Fig. 2 Comparison of the processing results of Sintogrind grinding oil with OEL-HELD and other products
a: Grinding effect of other grinding oils and conventional grinding wheels b: Grinding effect of other grinding oils and internally cooled grinding wheels c: Grinding effect of Sintogrind and internally cooled grinding wheels
The grinding oil is based on a base oil and is blended by adding various additives with different properties and functions to the base oil. At present, the world's best performance grinding oil base oil is a poly-α-olefin directly synthesized from ethylene as a raw material. Due to the purity and homogeneity of the product, polyalphaolefins have unsurpassed superior properties of other base oils and are used as base oils under the harsh conditions of Formula One racing cars. As its composition is pure alkanes, it has excellent shear resistance and anti-aging stability and is very suitable for high-speed grinding processing.
Wei Xinyang from the OEL-HELD (China) Southwest representative said that its company's Sintogrind, Diagrind and Toolgrind series of high-performance grinding oils use poly-α-olefins and hydrocracked oils as base oils, which have low evaporation rate and no corrosion ( Including seals), good filterability, strong washability, high defoaming, high flash point, and high viscosity index. Thanks to the unique synergistic effect of friction modifiers, anti-wear additives, extreme pressure additives and antioxidants, the above series of grinding oils completely avoid the precipitation of metallic cobalt when machining hard alloys and have excellent shear resistance. And anti-aging stability, in the reduction of energy consumption and wheel wear, the tool surface will not produce any burns, thus achieving high-precision processing requirements and obtain a good surface finish, it is recommended by the vast majority of well-known grinding machine manufacturers, In Europe and the United States and other countries, the market holds a major share.
Applications
In order to demonstrate the effect of a fully synthetic product based on polyalphaolefins, OEL-HELD conducted a series of tests at Rappold Winterthur Grinder. The grinded product was scanned with the same magnification using an electron microscope. As shown in Figure 2, a very high surface quality can be achieved with the Sintogrind total synthesis product.
Deyang Dong Auto Industry and Engineering Co., Ltd. has been using OEL-HELD's grinding oil products. Hu Jianhua, Vice Minister of Technology Development of the company, told the journal that OEL-HELD's grinding oil has been used for three years without replacement, effectively reducing The cost of production and equipment downtime will improve overall production efficiency.
Cutting
In recent years, the development and change of metal cutting fluids are mainly in the field of water-soluble liquids. This kind of liquid uses water as the matrix and has a high heat transfer rate (water has a heat transfer rate 2.5 times that of oil). After the same amount of water absorbs certain heat, it will be much slower than the temperature rise of the oil, thereby improving the cooling effect and reducing the oil mist. Therefore, the amount of water-based cutting fluid increases.
Currently, water-based cutting fluid accounts for about 60% of the total cutting fluid market in China. However, there are some problems in water-based cutting fluids compared to oils, including poor lubricity, as well as corrosion, colloidal stability, chemical stability, and biological stability. Problems such as sex, filterability, foaming, etc. These factors are crucial for the "sump life" of cutting fluids in machine tool applications.
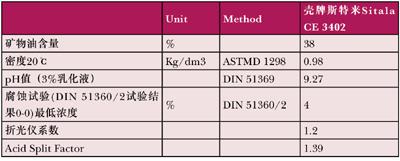
Table 2 Typical values ​​of Shell Stella C3402 water-soluble cutting fluid
Shell's Shell's Sitala CE 3402 high-performance water-soluble cutting fluid (see Table 2) contains a large number of extreme pressure additives and is suitable for the processing of steel and aluminum alloy materials. It can meet the demanding processing with high surface precision, as well as the high pressure and the use of internal cold cutting tools such as deep hole drilling, drilling, milling, and MARAL reaming.
Shell Stella Sitala CE 3402 has good anti-foam properties, excellent biological stability and cleaning performance, can keep the machine and workpiece clean. Its good cooling and lubricating properties ensure high precision of the machined workpiece. At the same time, Sitala CE 3402 has excellent biological stability and long product life, which can significantly reduce maintenance costs. The high corrosion resistance is beneficial for protecting tools, workpieces and guides.
User testimonials
BYD Precision Manufacturing Co., Ltd. has been using Shell's Sitala CE 3402 high-performance water-soluble cutting fluid during its manufacturing process. According to Zhang Qibo, the company's equipment department, this product has a long replacement cycle and a high cost performance compared to similar products. And it excels in protecting the tool and ensuring the precision of the machined workpiece.
Mr. Zhang deeply understood that the further development of production put forward higher requirements on the performance of metalworking fluids, such as enhancing maintainability and extending the replacement cycle, and so on. The ability of Shell Metalworking Fluid to meet this requirement is unique.
Energy conservation and environmental protection, cost reduction and efficiency increase are unstoppable
Experts of the Shenzhen Mould Technology Society, companies must fully weigh the advantages and disadvantages when selecting metalworking fluids, and must meet the following requirements: large heat capacity, good thermal conductivity, and good cooling effect. With high oiliness or strong metal surface adsorption, the formed adsorption film can have higher strength, and it can be adsorbed on the metal surface and play a good role in lubrication. If the anti-adhesiveness is good, it will not corrode the metal, and it will not damage the precision and surface roughness of the machine tool and workpiece due to corrosion. At the same time, products with low surface tension are prone to uniform diffusion, which is beneficial to cooling and washing and has good lubricity.
At the same time, experts said that economic cost considerations are also very important. The metalworking fluid must be easy to use, low in cost, easy to configure and best suited to a wide range of metal materials and various processing methods (eg, vehicles, grinding, planing, etc.), have a certain degree of transparency, and do not emit smoke when increasing the cutting speed. . It is harmless to the human body, non-toxic and odorless. Does not harm the skin and nasal mucosa, does not stimulate the eyes and so on. Good stability and long service life. During long-term use and storage, there is no delamination, no precipitation, no mildew. The amount of cutting waste liquid is large. Consider waste liquid treatment to avoid environmental pollution.
China’s policy measures to “preserve growth and expand domestic demand†are being implemented, key industry revitalization plans have also been introduced, the purchasing power of mold companies is increasing, the product types needed for business transformation will be more extensive, and the quality requirements for products will surely be rapid. improve. Under the test of the economic crisis, the needs of users of metalworking fluids in the mold industry are bound to accelerate toward the direction of high-efficiency, energy-saving, environmental-friendly and low-cost economics.
The most basic functions of metalworking fluids are lubrication, cooling, chip removal and protection. These four properties are not completely isolated. They have both a unified surface and an opposite surface. Such as cutting oil lubrication, anti-performance is good, but poor cooling, cleaning; aqueous solution, cooling, washing performance is good, but poor lubrication and anti-performance.
It is generally believed that in the low-speed heavy-load cutting machining (thread cutting, reaming, and tooth cutting), sufficient lubrication is required, and the extreme pressure cutting oil is usually selected. The main task of the cutting lubricant is to reduce the adhesion between the advancing surface and the chips. , as a boundary lubricant. In high-speed shallow cutting, cooling is the first choice. Water-based cutting fluid is generally used. Its main function is to reduce frictional heat and to remove heat. Those machining fluids that are difficult to reach the shear zone cause great difficulty in lubrication and cooling. Generally, suitable cutting fluids are carefully selected for reaming, gear cutting (especially hobbing), deep-hole drilling and boring, tapping (especially blind holes), deep-set holes, and threading.
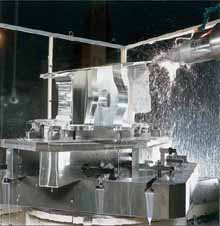
Fig. 1 The application of metalworking fluids in production shows that the use of suitable metalworking fluids can reduce the cutting temperature by 60~150°C, reduce the surface roughness by 1~2 grades, reduce the cutting resistance by 15~30%, and double the improvement. The service life of the cutters and grinding wheels, as well as the removal of iron chips and ash from the cutting area, increases the productivity and product quality.
In the mold processing process, the role of the tool is to cut off the processed material with a strong shear force in the main shear zone. Between the advancing surface of the tool and the exposed fresh metal surface, the thrust surface is subjected to high stress due to the strong adhesion. The cutting flaking due to cutting cuts through the tool advancing surface, creating a second shear zone - the shearing action of this area gives the tool maximum friction. At this time, the importance of lubrication and cooling is highlighted at the same time. It is worth noting that there are many types of metal removal machining, and each has its own unique working conditions.
The following will focus on the application of metalworking fluids in three specific processing methods, and combined with the user interview reports of Shell, De &22269, and OEL-HELD in this publication to illustrate the specifics of metalworking fluids. Application and performance requirements.
EDM
Shell's Wanan EDM110 and 130 are high-quality spark erosion machining oils (see Table 1, continued on the next page). They are made of paraffin-based base oils with high precision refining and very low aromatic content, good insulation properties, and product processing. High precision, long life, little skin irritation. Among them, the former has a medium viscosity and is suitable for spark erosion processing; the latter has a high viscosity and is suitable for high precision machining of spark erosion. Both of these products can also be used as tool grinding oils.
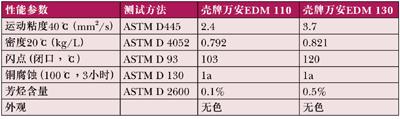
Table 1 Typical Value of Shell EDM 110/130 Spark Erosion Process Oil
Shell Wanan EDM110 and Shell Wanan EDM130 have some of the same features: low viscosity, excellent cleaning of workpieces and spark plugs; good chip resistance, extended electrode life; good insulation, high dielectric strength, surface finish High precision, processing surface roughness can be as low as 3 microns to lower; high flash point, can reduce the risk of fire in the machine; high boiling point, minimize volatilization losses, prevent oil viscosity due to volatile loss and processing accuracy Drop; good thermal stability and oxidation stability, long service life, not easy to oxidation and discoloration; colorless and odorless, help users to observe the process of spark plug processing; good filterability, rapid removal of fine processing Crumbs; aromatics content is extremely low, little effect on skin irritation, harmless to the human body.
User testimonials
Shell metal processing oil / liquid performance, product life cycle. In this regard, BYD Precision Manufacturing Co., Ltd. Equipment Department Zhang Qibo has a deep understanding.
According to Zhang Qibo, BYD precision manufacturing is one of the top three mold manufacturing bases in South China, and its equipment department has hundreds of well-known brand machine tools. The company's current use of Shell Spark Erosion Process Oil has been over three and a half years, and it has no discoloration or taste change. With such a long service life, BYD Company has not only reduced the procurement cost of oil products, but also effectively reduced equipment downtime due to oil changes, thus realizing improved production efficiency.
Not only that, the use of Shell spark erosion processing oil, also provides an effective guarantee for BYD's production safety. BYD's technicians had done such an experiment—the use of cloth strips to dip shell sparks to etch the oil, and then tried to light it, but after many tests, the strips could not be burned. It can be seen that compared with other kerosene spark erosion processing oils, Shell spark erosion machining oil has stable performance and is a reliable guarantee for safe production.
Grinding
The friction between the abrasive particles and the metal surface during the grinding process generates a lot of heat. When the heat is accumulated to a certain degree (the instantaneous temperature of the grinding point can reach 1500°C, and the average temperature of the grinding area of ​​the abrasive and the workpiece is between 500°C and 800°C), the surface of the workpiece will be burned or even deformed. The surface quality and accuracy will be affected. If the operating conditions of the grinding process are improved and the grinding oil is used for sufficient cooling and lubrication, half of the thermal energy in the process will be absorbed by the coolant, and the final heat input to the workpiece will only account for 15% of the heat energy generated during the entire process. . Therefore, the grinding oil effectively reduces the chance of the workpiece being burned.
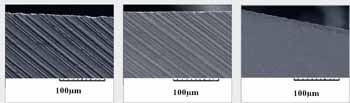
Fig. 2 Comparison of the processing results of Sintogrind grinding oil with OEL-HELD and other products
a: Grinding effect of other grinding oils and conventional grinding wheels b: Grinding effect of other grinding oils and internally cooled grinding wheels c: Grinding effect of Sintogrind and internally cooled grinding wheels
The grinding oil is based on a base oil and is blended by adding various additives with different properties and functions to the base oil. At present, the world's best performance grinding oil base oil is a poly-α-olefin directly synthesized from ethylene as a raw material. Due to the purity and homogeneity of the product, polyalphaolefins have unsurpassed superior properties of other base oils and are used as base oils under the harsh conditions of Formula One racing cars. As its composition is pure alkanes, it has excellent shear resistance and anti-aging stability and is very suitable for high-speed grinding processing.
Wei Xinyang from the OEL-HELD (China) Southwest representative said that its company's Sintogrind, Diagrind and Toolgrind series of high-performance grinding oils use poly-α-olefins and hydrocracked oils as base oils, which have low evaporation rate and no corrosion ( Including seals), good filterability, strong washability, high defoaming, high flash point, and high viscosity index. Thanks to the unique synergistic effect of friction modifiers, anti-wear additives, extreme pressure additives and antioxidants, the above series of grinding oils completely avoid the precipitation of metallic cobalt when machining hard alloys and have excellent shear resistance. And anti-aging stability, in the reduction of energy consumption and wheel wear, the tool surface will not produce any burns, thus achieving high-precision processing requirements and obtain a good surface finish, it is recommended by the vast majority of well-known grinding machine manufacturers, In Europe and the United States and other countries, the market holds a major share.
Applications
In order to demonstrate the effect of a fully synthetic product based on polyalphaolefins, OEL-HELD conducted a series of tests at Rappold Winterthur Grinder. The grinded product was scanned with the same magnification using an electron microscope. As shown in Figure 2, a very high surface quality can be achieved with the Sintogrind total synthesis product.
Deyang Dong Auto Industry and Engineering Co., Ltd. has been using OEL-HELD's grinding oil products. Hu Jianhua, Vice Minister of Technology Development of the company, told the journal that OEL-HELD's grinding oil has been used for three years without replacement, effectively reducing The cost of production and equipment downtime will improve overall production efficiency.
Cutting
In recent years, the development and change of metal cutting fluids are mainly in the field of water-soluble liquids. This kind of liquid uses water as the matrix and has a high heat transfer rate (water has a heat transfer rate 2.5 times that of oil). After the same amount of water absorbs certain heat, it will be much slower than the temperature rise of the oil, thereby improving the cooling effect and reducing the oil mist. Therefore, the amount of water-based cutting fluid increases.
Currently, water-based cutting fluid accounts for about 60% of the total cutting fluid market in China. However, there are some problems in water-based cutting fluids compared to oils, including poor lubricity, as well as corrosion, colloidal stability, chemical stability, and biological stability. Problems such as sex, filterability, foaming, etc. These factors are crucial for the "sump life" of cutting fluids in machine tool applications.
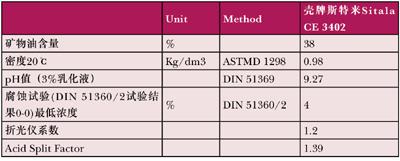
Table 2 Typical values ​​of Shell Stella C3402 water-soluble cutting fluid
Shell's Shell's Sitala CE 3402 high-performance water-soluble cutting fluid (see Table 2) contains a large number of extreme pressure additives and is suitable for the processing of steel and aluminum alloy materials. It can meet the demanding processing with high surface precision, as well as the high pressure and the use of internal cold cutting tools such as deep hole drilling, drilling, milling, and MARAL reaming.
Shell Stella Sitala CE 3402 has good anti-foam properties, excellent biological stability and cleaning performance, can keep the machine and workpiece clean. Its good cooling and lubricating properties ensure high precision of the machined workpiece. At the same time, Sitala CE 3402 has excellent biological stability and long product life, which can significantly reduce maintenance costs. The high corrosion resistance is beneficial for protecting tools, workpieces and guides.
User testimonials
BYD Precision Manufacturing Co., Ltd. has been using Shell's Sitala CE 3402 high-performance water-soluble cutting fluid during its manufacturing process. According to Zhang Qibo, the company's equipment department, this product has a long replacement cycle and a high cost performance compared to similar products. And it excels in protecting the tool and ensuring the precision of the machined workpiece.
Mr. Zhang deeply understood that the further development of production put forward higher requirements on the performance of metalworking fluids, such as enhancing maintainability and extending the replacement cycle, and so on. The ability of Shell Metalworking Fluid to meet this requirement is unique.
Energy conservation and environmental protection, cost reduction and efficiency increase are unstoppable
Experts of the Shenzhen Mould Technology Society, companies must fully weigh the advantages and disadvantages when selecting metalworking fluids, and must meet the following requirements: large heat capacity, good thermal conductivity, and good cooling effect. With high oiliness or strong metal surface adsorption, the formed adsorption film can have higher strength, and it can be adsorbed on the metal surface and play a good role in lubrication. If the anti-adhesiveness is good, it will not corrode the metal, and it will not damage the precision and surface roughness of the machine tool and workpiece due to corrosion. At the same time, products with low surface tension are prone to uniform diffusion, which is beneficial to cooling and washing and has good lubricity.
At the same time, experts said that economic cost considerations are also very important. The metalworking fluid must be easy to use, low in cost, easy to configure and best suited to a wide range of metal materials and various processing methods (eg, vehicles, grinding, planing, etc.), have a certain degree of transparency, and do not emit smoke when increasing the cutting speed. . It is harmless to the human body, non-toxic and odorless. Does not harm the skin and nasal mucosa, does not stimulate the eyes and so on. Good stability and long service life. During long-term use and storage, there is no delamination, no precipitation, no mildew. The amount of cutting waste liquid is large. Consider waste liquid treatment to avoid environmental pollution.
China’s policy measures to “preserve growth and expand domestic demand†are being implemented, key industry revitalization plans have also been introduced, the purchasing power of mold companies is increasing, the product types needed for business transformation will be more extensive, and the quality requirements for products will surely be rapid. improve. Under the test of the economic crisis, the needs of users of metalworking fluids in the mold industry are bound to accelerate toward the direction of high-efficiency, energy-saving, environmental-friendly and low-cost economics.
Compound Material Force Control System
Our compound Force Control System, compound active contact flange, compound Constant Force Actuator have many advantages over other grinders. It can realize flexible grinding, quick repsond to surface changing, and instant adjusting. Traditional mechanic hand lacks flexibility, and it is not easy to adjust, hard to realize mass production.
Compound force control system, compound active contact flange, compound constant force actuator
DARU Technology (Suzhou) Co., Ltd. , https://www.szactivecontactflange.com